My first goal for this project is to have a rolling chassis I can push around the garage by the end of the year. To that end, I’ve picked up a GS650L front end. But lots of things are dependent on lots of other things —*rake and trail are dependent on fork length, which also affects ride height, which is also determined by the choice of rear shock and how that’s mounted, etc…
So, I’m starting with the most basic task, attaching the swingarm to the chassis. The YZ125C swingarm may be nicely braced and ready to accept a high-mounted monoshock, but it has one major drawback that makes it a less-than-ideal choice: it uses a really wimpy 12mm swingarm pivot bolt. I initially played with the idea of going with a larger diameter bolt, especially when I discovered that the 15mm Suzuki front axle I have is just the right length for the Bul frame (which is about 27mm wider at the mounts than the swingarm). But the ID of the swingarm’s mounting tube is only slightly less than 24mm, so there’s just not enough room to go thicker on the bolt. If I used a 15mm bolt, the inner and outer bushing surfaces would have to be no thicker than 12 or 14 gauge sheetmetal to fit in there. Wafer-thin bushings would be no better than the skinny bolt. So, I’m stuck with a 12mm bolt and the stock Yamaha nylon bushings. Realistically, that shouldn’t be a problem. I’ll most likely end up with a motor that doesn’t put out too much more than the YZ’s original 18 HP, and street use won’t stress it like banging hard landings off whoops and doubles would.
The Bul originally used the swingarm pivot for the rear motor mount. Considering the skinny pivot bolt I’ll be using, and the fact that the Yamaha swingarm would have to have a gap cut out of the center to accomodate it, I’ve decided to let the swingarm design dictate alternative engine mounting, rather than the other way around. After all, I have yet to even determine exactly what engine is going to power this thing. (Like I said up top, every decision affects another decision down the line, so the order you do things makes a big difference.)
I am, however, now presented with a separate issue —*the swingarm mounting holes in the Bultaco frame are 14.3mm in diameter:
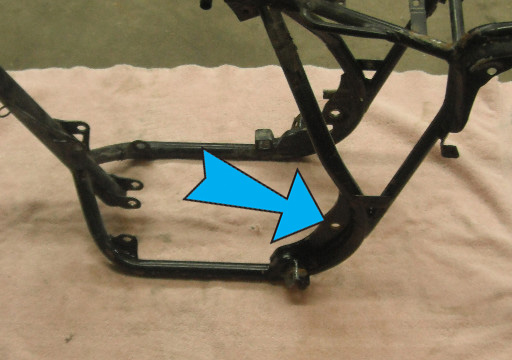
So, how do I “drill them smaller” to center the pivot bolt? Several people have said, “make up spacers,” but don’t think collars 1.15mm thick and as wide as the mounting plates are a practical option. I could weld up the hole and then drill it out to the proper size, but how do I ensure the two sides stay in alignment? Like most guys, I don’t have any high-accuracy stuff like a jig or machine tools.
Right now I’m thinking that I could weld a pair of proper diameter washers to the frame on either side of the mounting holes. I don’t have to center the pivot bolt in the existing holes, I just have to keep it aligned horizontally in the frame. So I could simply install the washers on the pivot bolt and let the bolt rest on the bottom of the holes in the frame while I welded them. (Note that the gap is at the top in the diagram below.) Once I torqued the pivot bolt down, I’m assuming that there’d be a lot of compression friction keeping things in place, so that the welds wouldn’t bear too much of the stress directly.
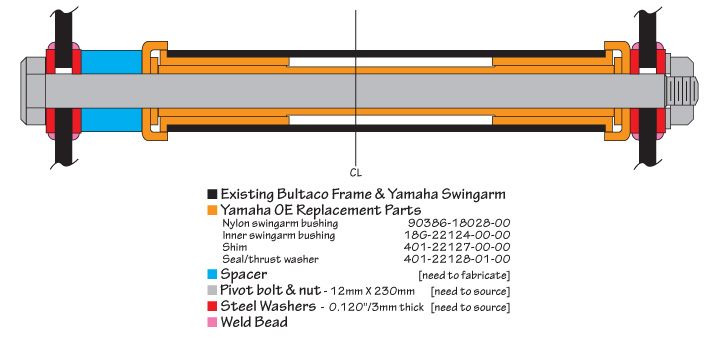
This all seems workable, but two questions came to mind:
- Is my washer idea any good? How thick do they need to be, and could I get by with only welding them on one side?
- Where do I source a strong 12mm bolt about 230mm long?
Well, duh. The answers were something I had not considered: using the Suzuki axle as a pivot bolt and simply having it turned down to 12mm. The threaded portion is already necked down as it is.

I could simply use an expanding reamer to enlarge the right side frame hole to fit the axle’s original diameter, have the spacer made up with a 15mm bore, and have the axle turned down far enough along its length to accomodate the swingarm. I’d have to take more care to make sure that I welded the washers onto the other side of the frame in the proper alignment, but I am thinking a few 90-degree magnetic holders and some careful measurements with a calipers before I weld should get me there.