I have successfully bent The Bride’s new frame downtubes to fit. Now I need to make slugs for the joints with the existing frame. But how do I go about inserting a slug into both ends of the tube simultaneously?
In the past, I have typically left a sizable gap between the tubes I was joining. That way, I could insert an extra-long slug into one tube, slide it partially into the other, and weld the slug separately to each tube. Unfortunately, that ends up with a skinnier section in the middle that looks pretty cobby. Since I already have two different tube diameters here, I really didn’t want to do that this time. So…
There may be more straightforward ways to do it, but here’s what I came up with:
First, I turned a couple of slugs that are the ID of the frame tubing on one side, and the smaller ID of my new tube on the other. Note that one of them has a little lip or collar in the middle, and one does not.

I bored a big hole in the bottom of the one without the retaining collar and soldered a length of 16 ga. automotive wire to it.
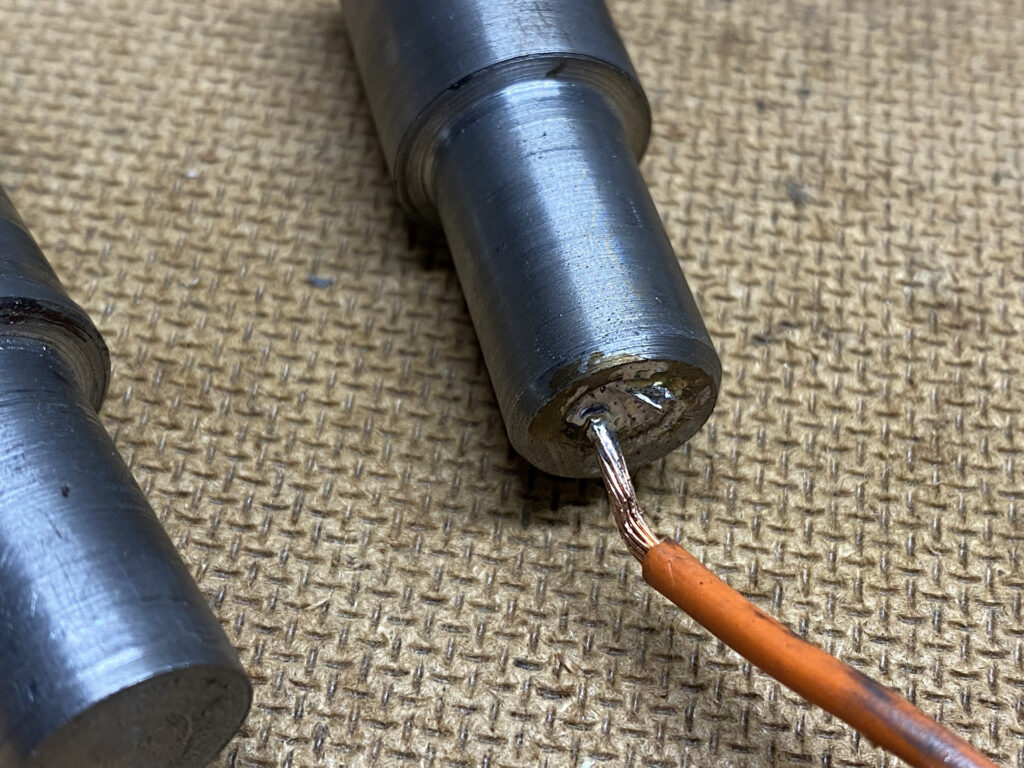
I drilled a small hole at the bend of the new tube, and threaded the wire through it. I also drilled a hole at the very end to create a notch for the wire.

On the bike, I fitted the slug and tube to the bottom frame tube first. The lip keeps the slug centered at the junction point.

At the other end, I slid the slug fully into the downtube, moved the tube into position, and then pulled on the wire. The difference in inside diameters prevents the slug from coming too far, and my little alignment marks show when it is fully seated. Gravity will help it stay in position until it gets welded.

And now it’s locked in place and ready for welding. Once I do the same operation on the other side, I will drill a couple of additional holes in the frame tubes and plug-weld each of the slugs through the holes on both sides of the joint.


Now to weld it up.
My little 85-amp Clarke spoolgun welder has a big bottle of 100% argon hooked up to it, which is great for welding aluminum and MIG brazing, but no bueno for MIG welding steel. I also have a H-F Titanium 125 gassless flux-core welder.
I’m undecided whether to:
- try my hand at silcon-bronze MIG brazing around the diameter of the joints;
- flux-core weld the whole thing with the Titanium 125;
- spend the money for a bottle of 25/75 MIG gas;
- or take the whole thing to my friendly neighborhood welding shop.